Heat Transfer Division
Waste heat units
Cyclotherm has been designing and manufacturing Heat Exchangers of all types for over 50 years.
Cyclotherm has been designing and manufacturing Heat Exchangers of all types for over 50 years.
Starting in 1965, special attention was directed toward Waste Heat Recovery Units, including Acid Gas Burning and Sulphur Recovery types. Since then we have supplied many such units, each individually tailored to the job requirements, whether it be one, two, three, four or five gas passes. Some were for steam production; some water heating in the normal 180°-200° temperature range and some for heating various glycol-water mixtures up to 350°F. Pressures ranged from 15# steam – 30# water to 300# steam.
The savings made possible by utilizing heat otherwise ignored or wasted, are shown on the curves on this brochure.
Put money in your pocket by utilizing Cyclotherm Waste Heat Technology. Let’s talk about the savings that can be yours. Contact us today!
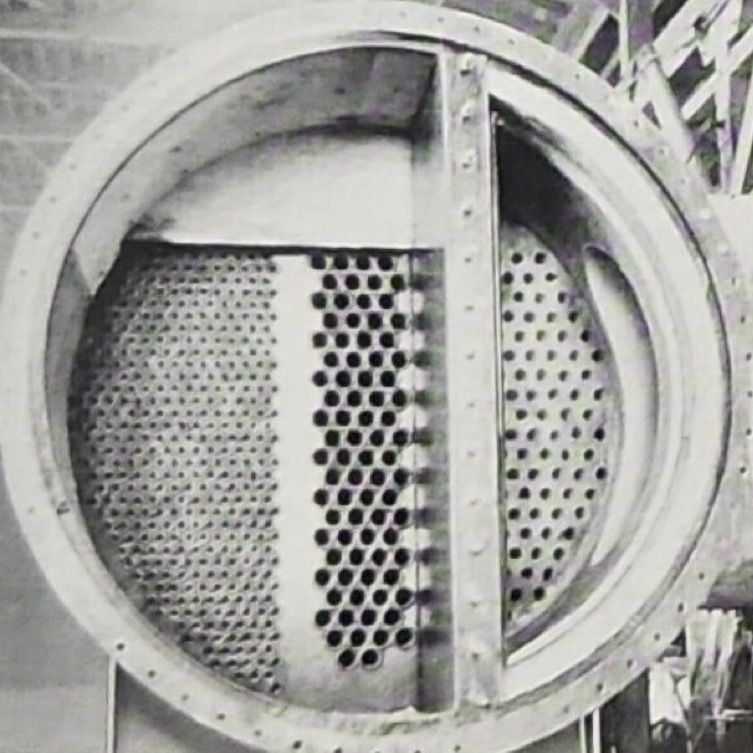
3 Pass – 200# W.P. Sulphur Plant Waste Heat Boiler – 25,000# steam per hour – 25 Tons sulphur recovery per day.
3 Pass – 200# W.P. Sulphur Plant Waste Heat Boiler – 25,000# steam per hour – 25 Tons sulphur recovery per day.
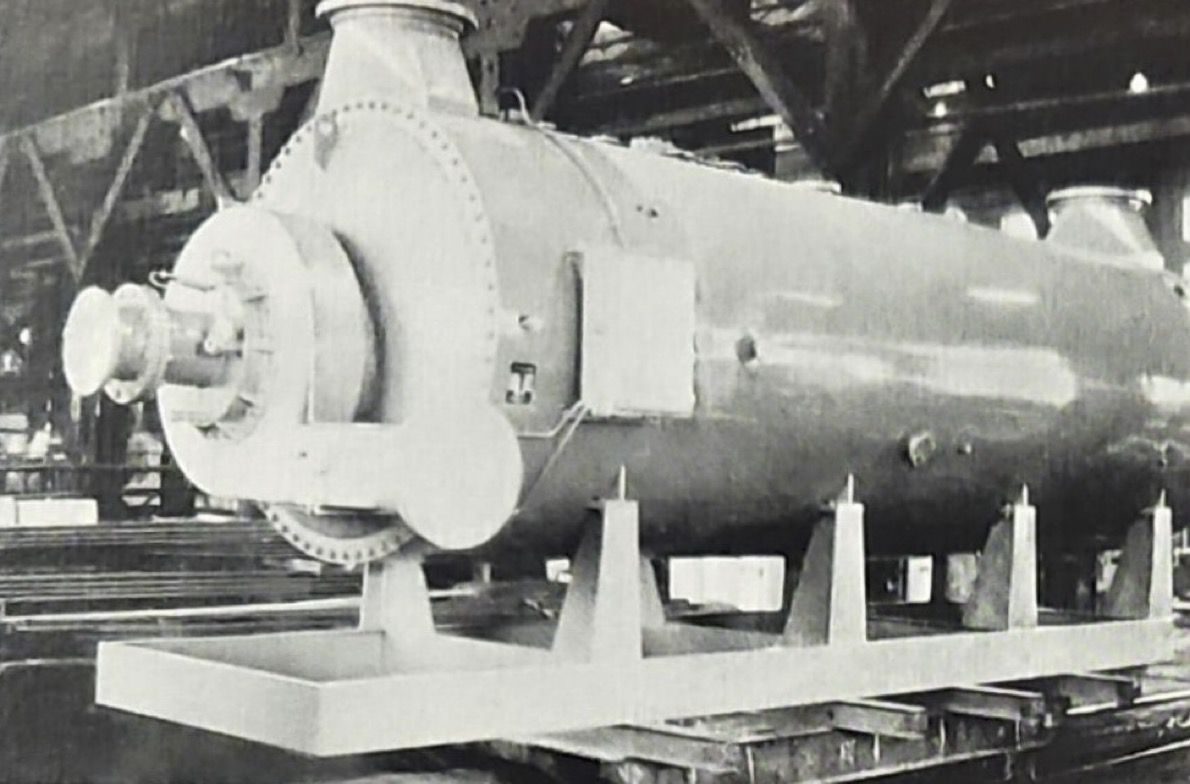
3 Pass – 300 #W.P. Hydrogen Sulfide Burners with Acid Gas Burner –20,000# Steam per hour – 100 tons/day Sulfur Recovery.
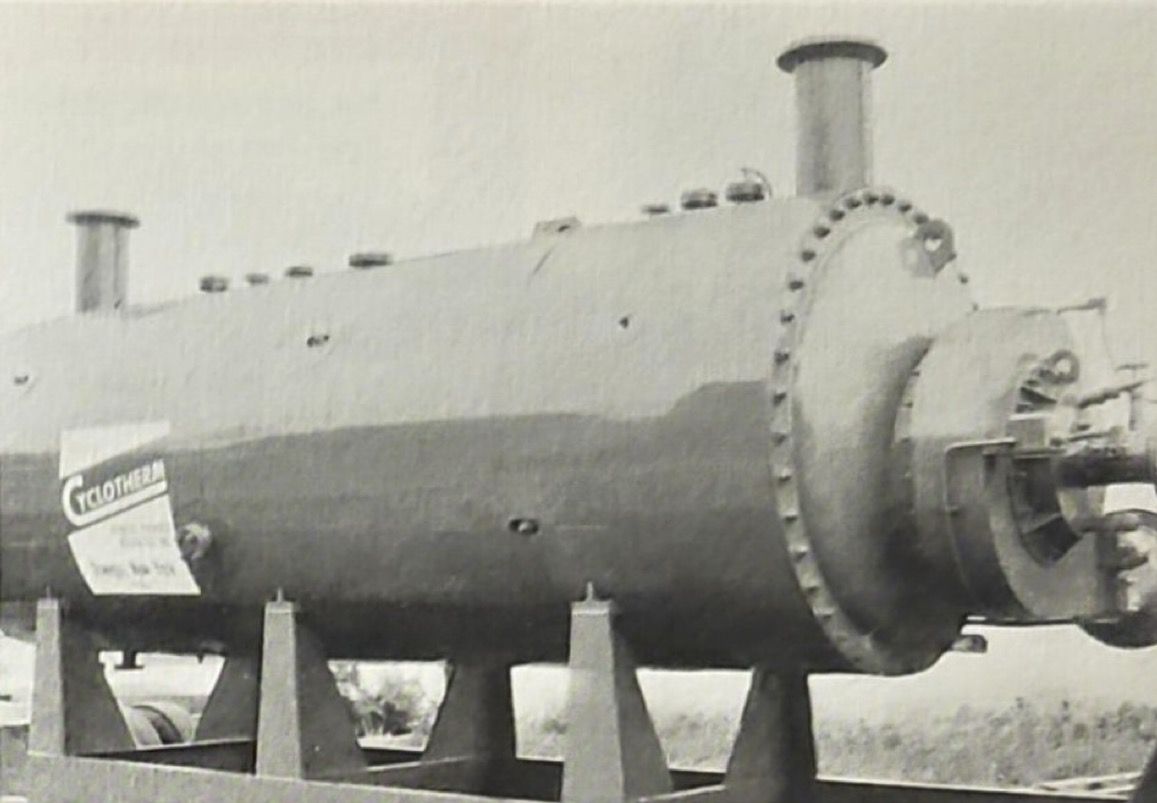
3 Pass – 300 #W.P. Sour Water Unit with burner – 4500# Steam per Hour.
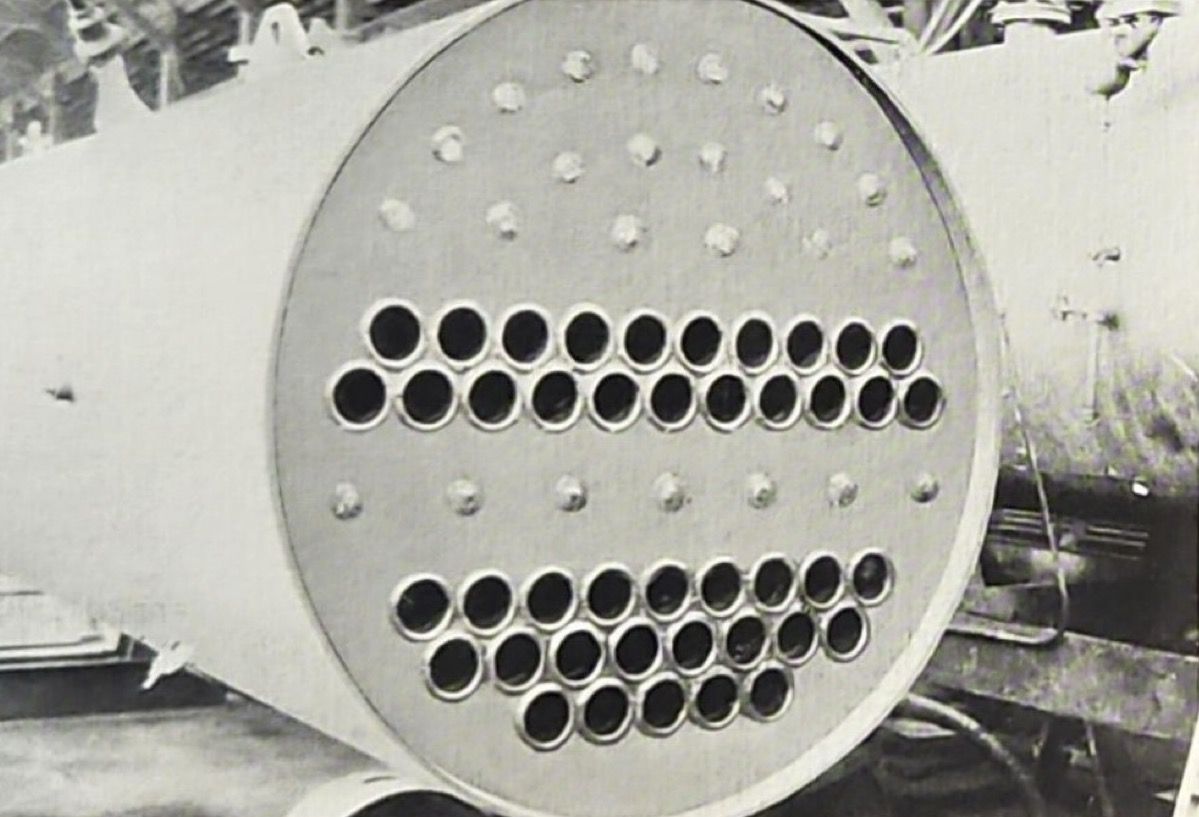
2 Pass – 200# W.P. Unit Recovery Waste Heat from silicate Furnace 7000# steam per hour.
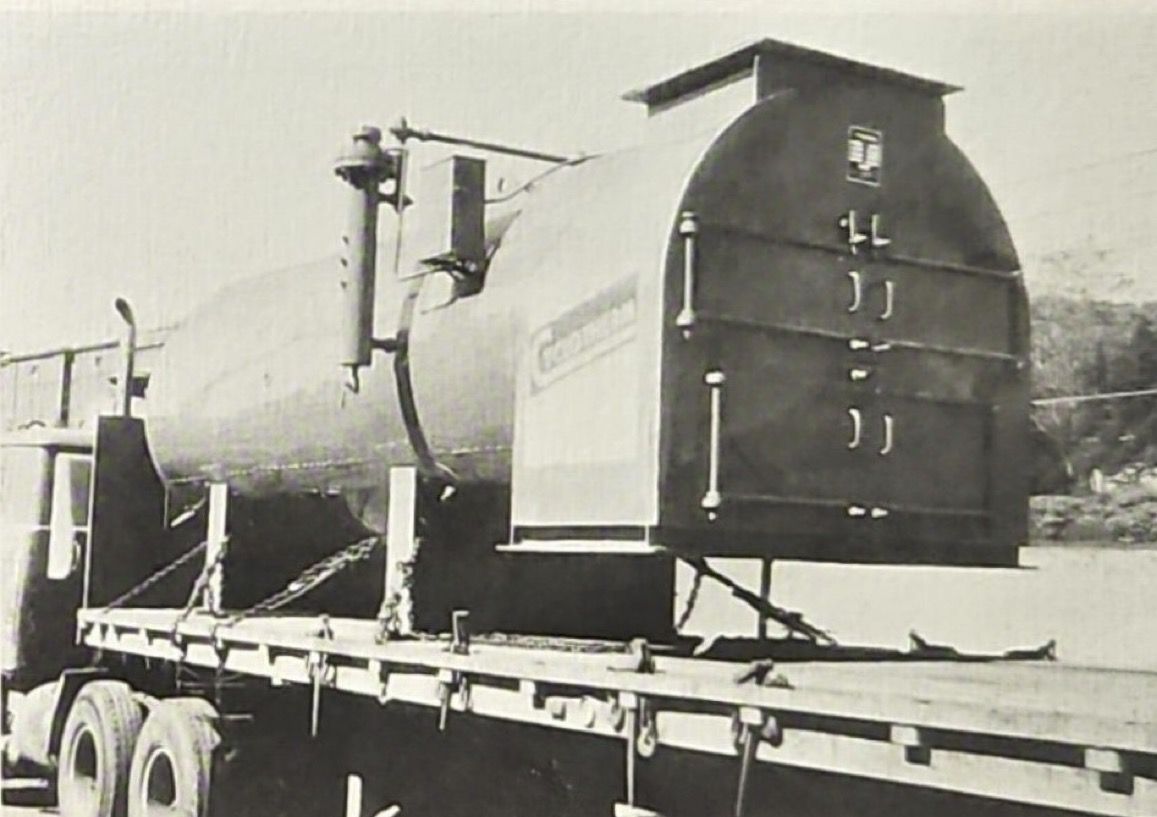
On truck ready for shipment.
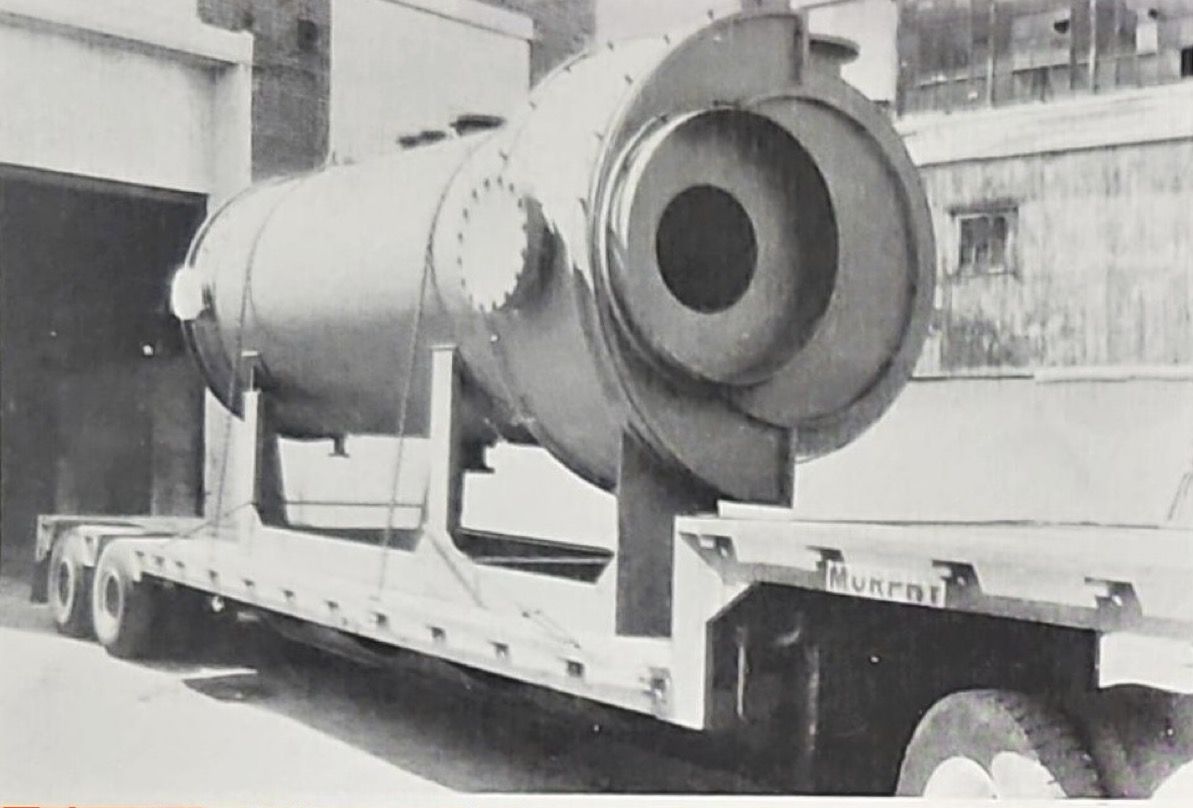
2 Pass – 200 #W.P. Sulphur plant Waste Heat Exchanger – using glycol water at 325°F to recover heat.
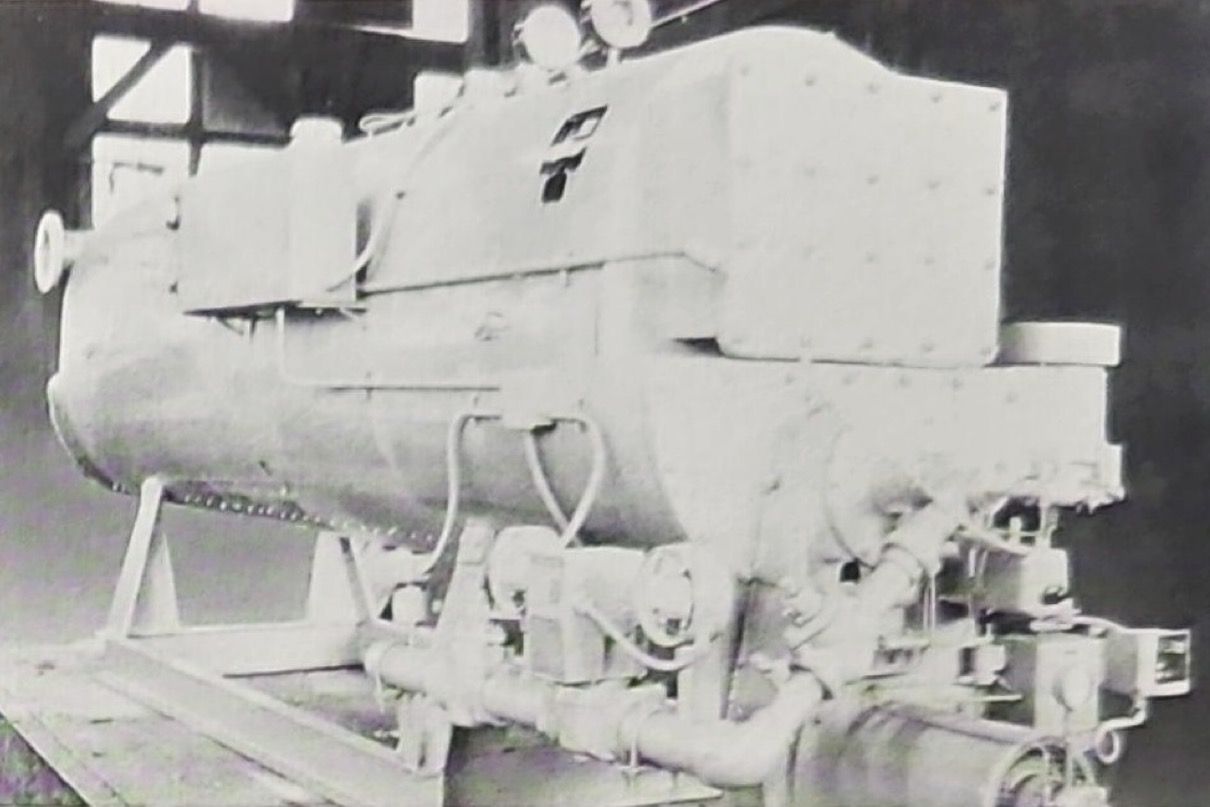
Sludge Heater for Sewage Treatment Plant – capacity 1,125,000 BTU/Hr. (available to 5,000,000 BTU/Hr) Burns Sewage Gas as available then automatically switching to alternate fuel.
Savings results from Waste Heat Recovery.
Savings results from Waste Heat Recovery.
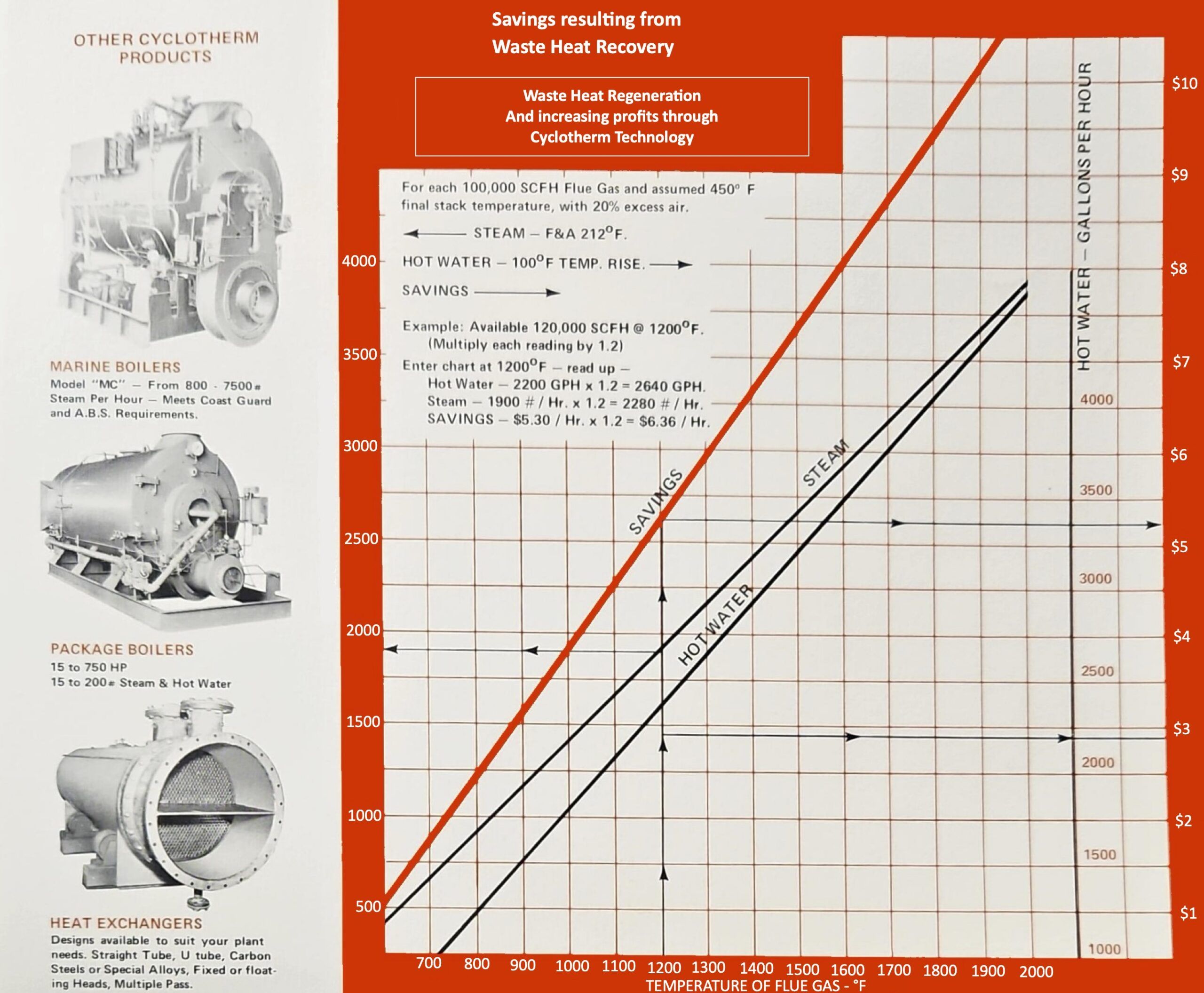
SULFURIC ACID PLANT HEAT EXCHANGERS
SULFURIC ACID PLANT HEAT EXCHANGERS
Typical small stainless Condensers. These are specially designed for each application. Similar units can be used for sulfuric acid cooling.
Views of high-pressure U tube vapor Condenser.
Views of high-pressure U tube vapor Condenser.
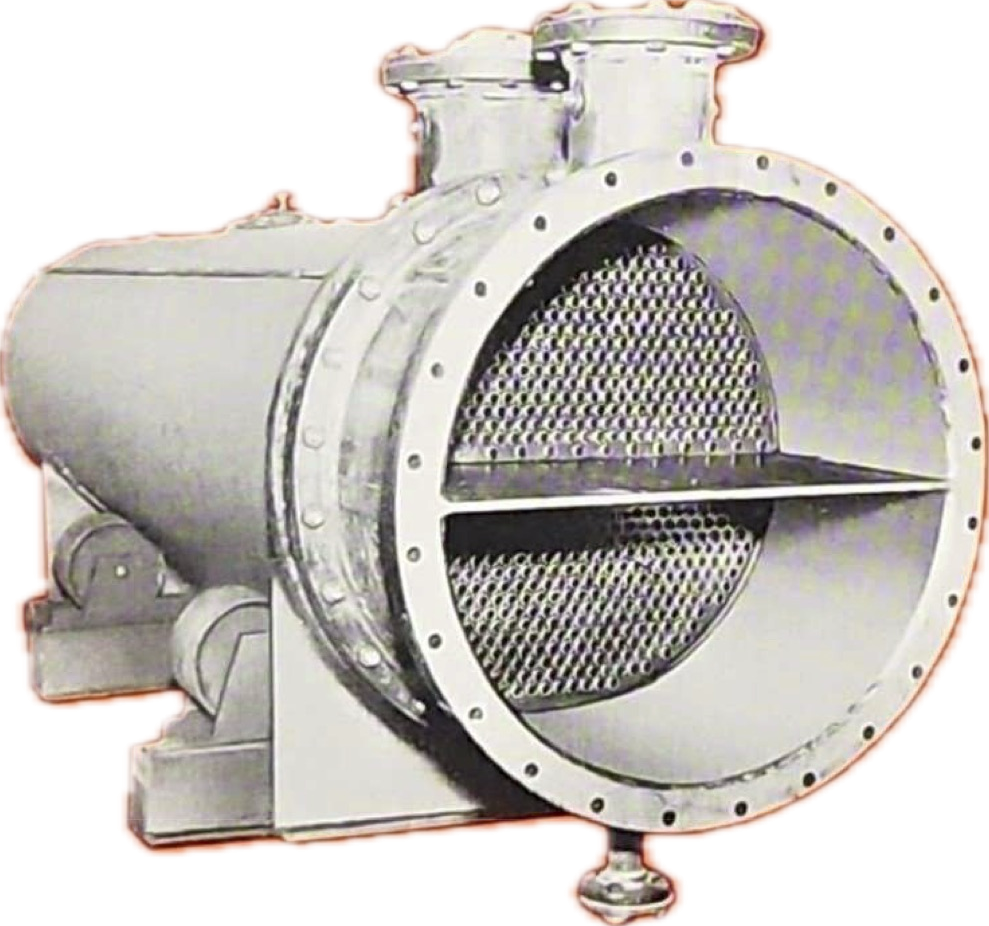
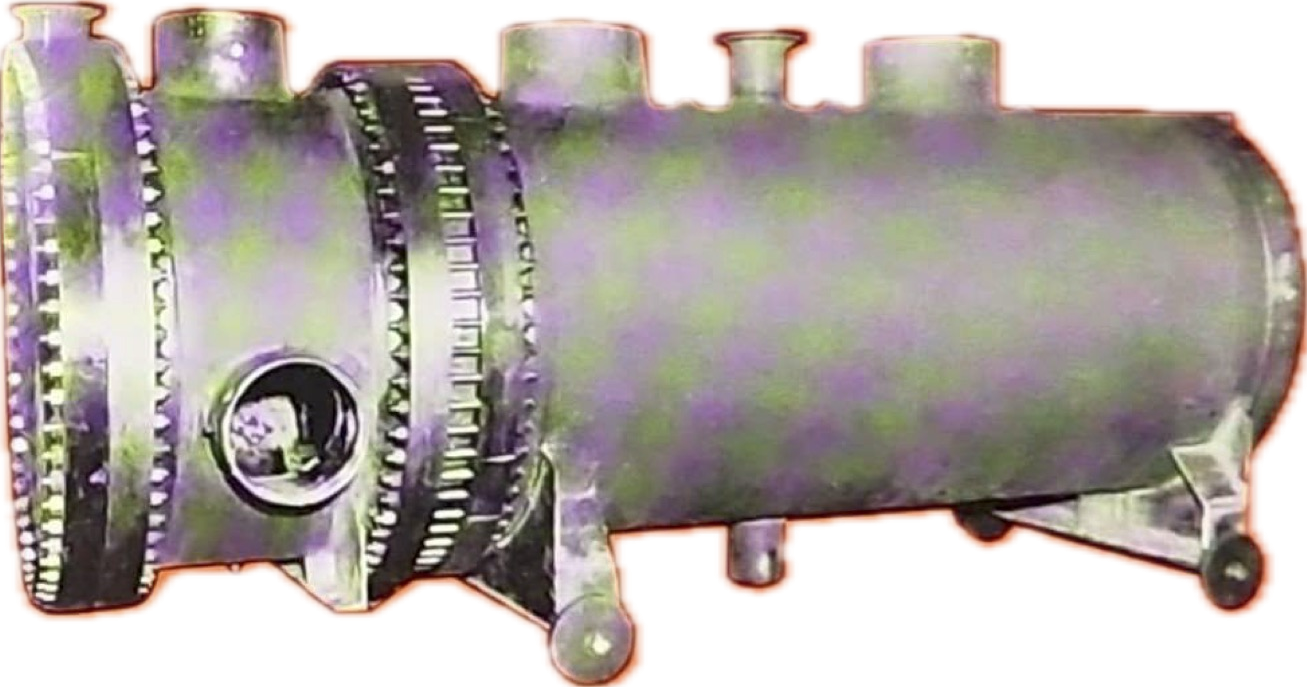
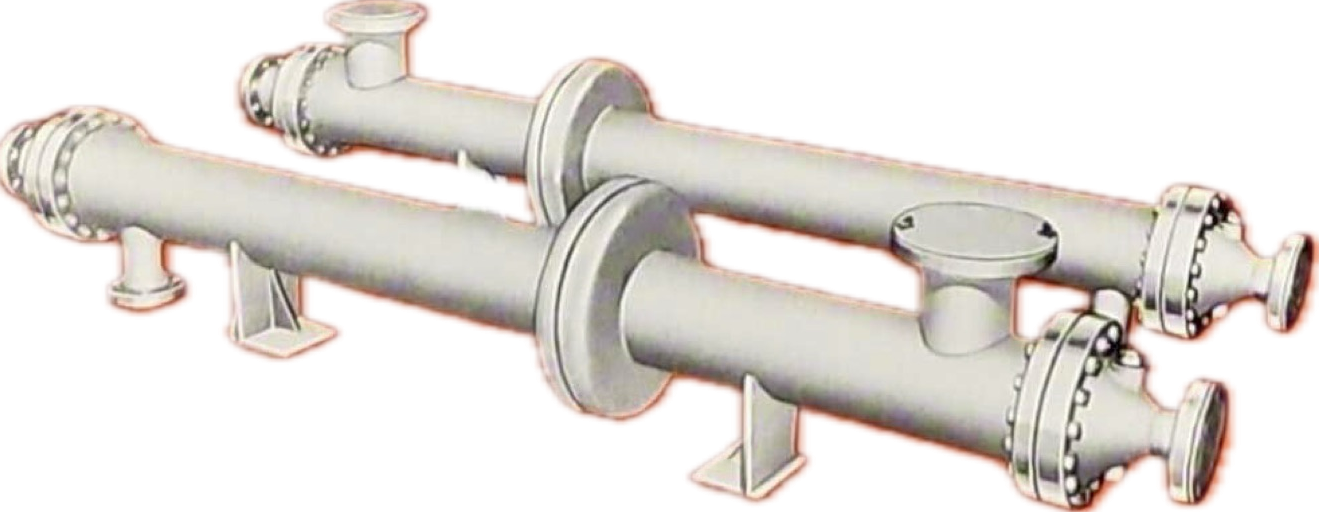
Sulfuric Acid Coolers
Shop views of typical medium size stainless steel H2SO4 coolers for contact plant absorber tower and drying tower service. Note single pass tube side construction to handle acid under optimum velocity and metal temperature conditions. This avoids the necessity of sophisticated electronic passivation and monitoring apparatus.
Water flows through shell in a divided flow configuration for maintaining tube side metal temperatures using abnormally warm water from a closed water to air cooling system. This type of installation is particularly suited for use in scarce water areas.
Note the oversized inlet distribution belts combined with shell expansion joints.
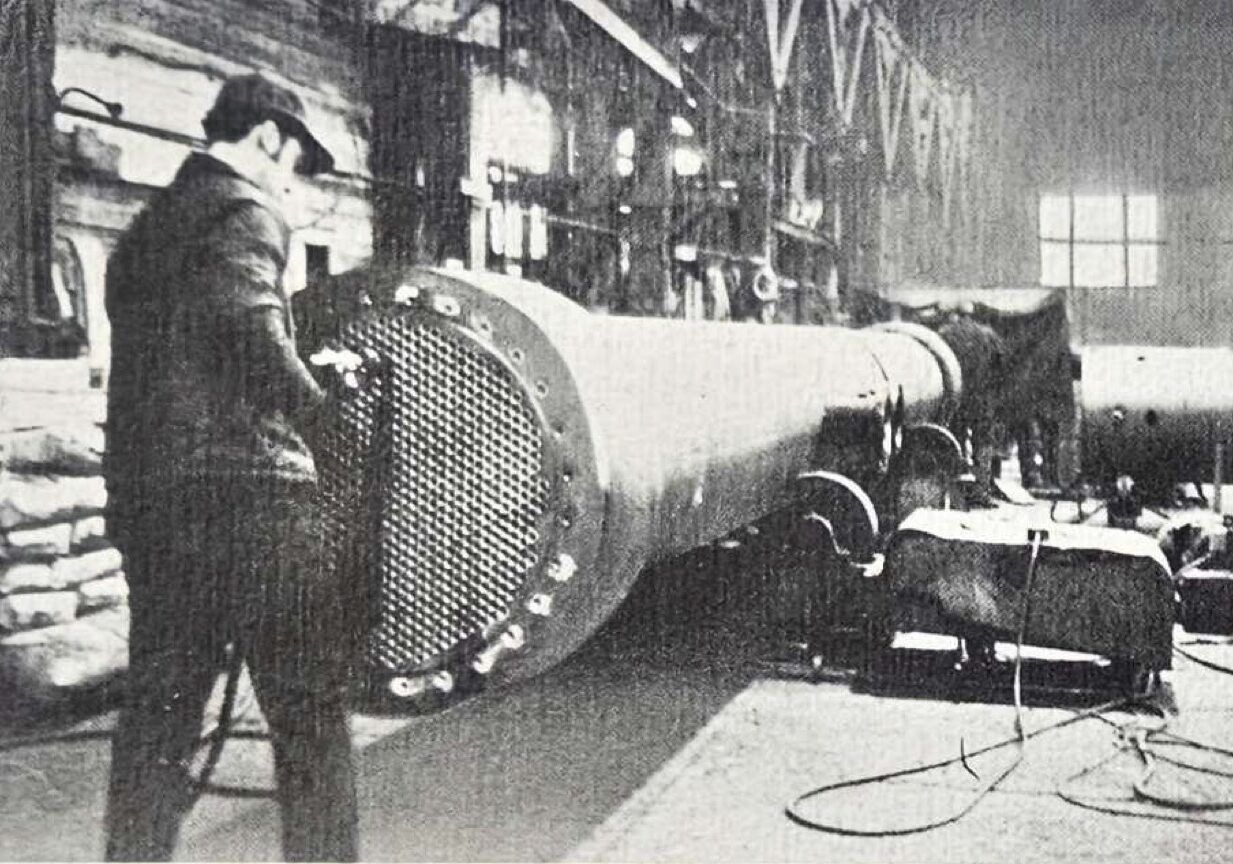
Seal rolling of tubes after TIG welding to tube sheets
Seal rolling of tubes after TIG welding to tube sheets
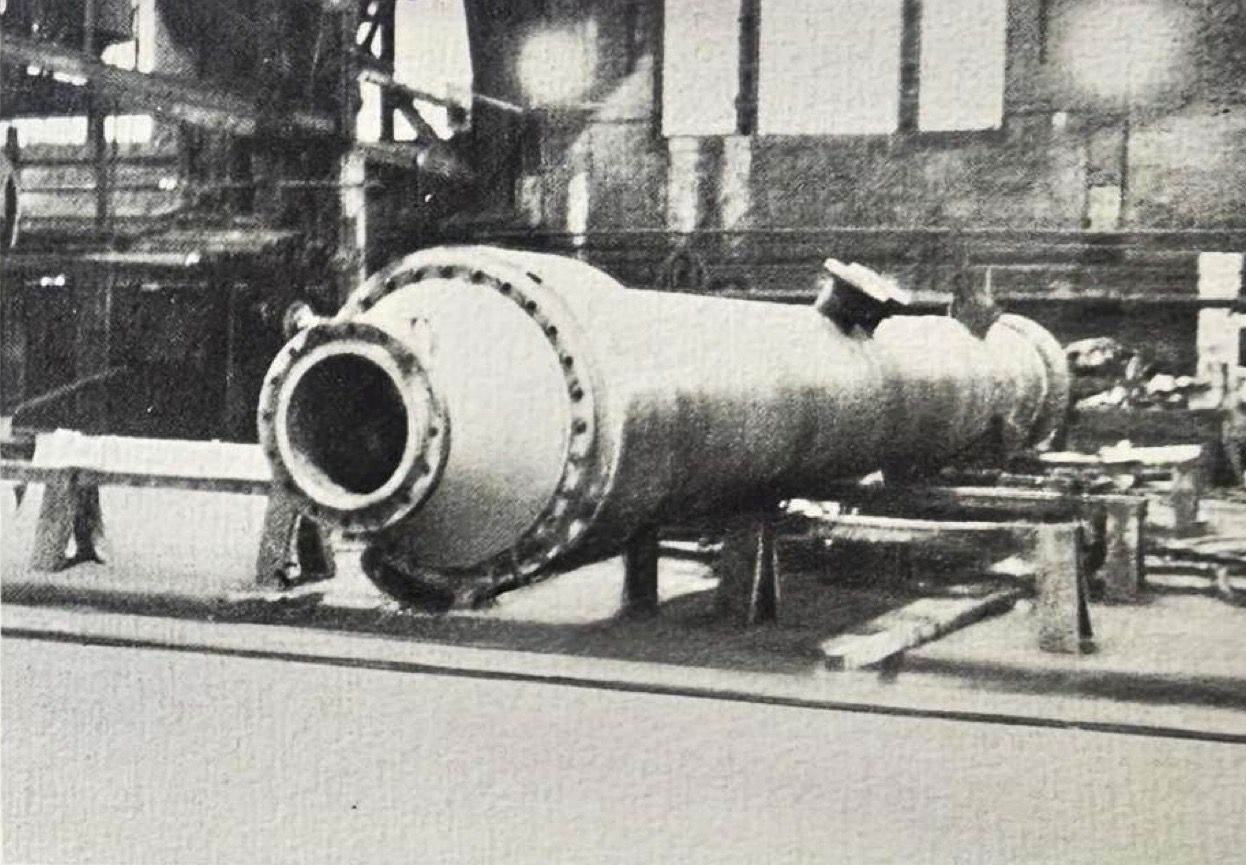
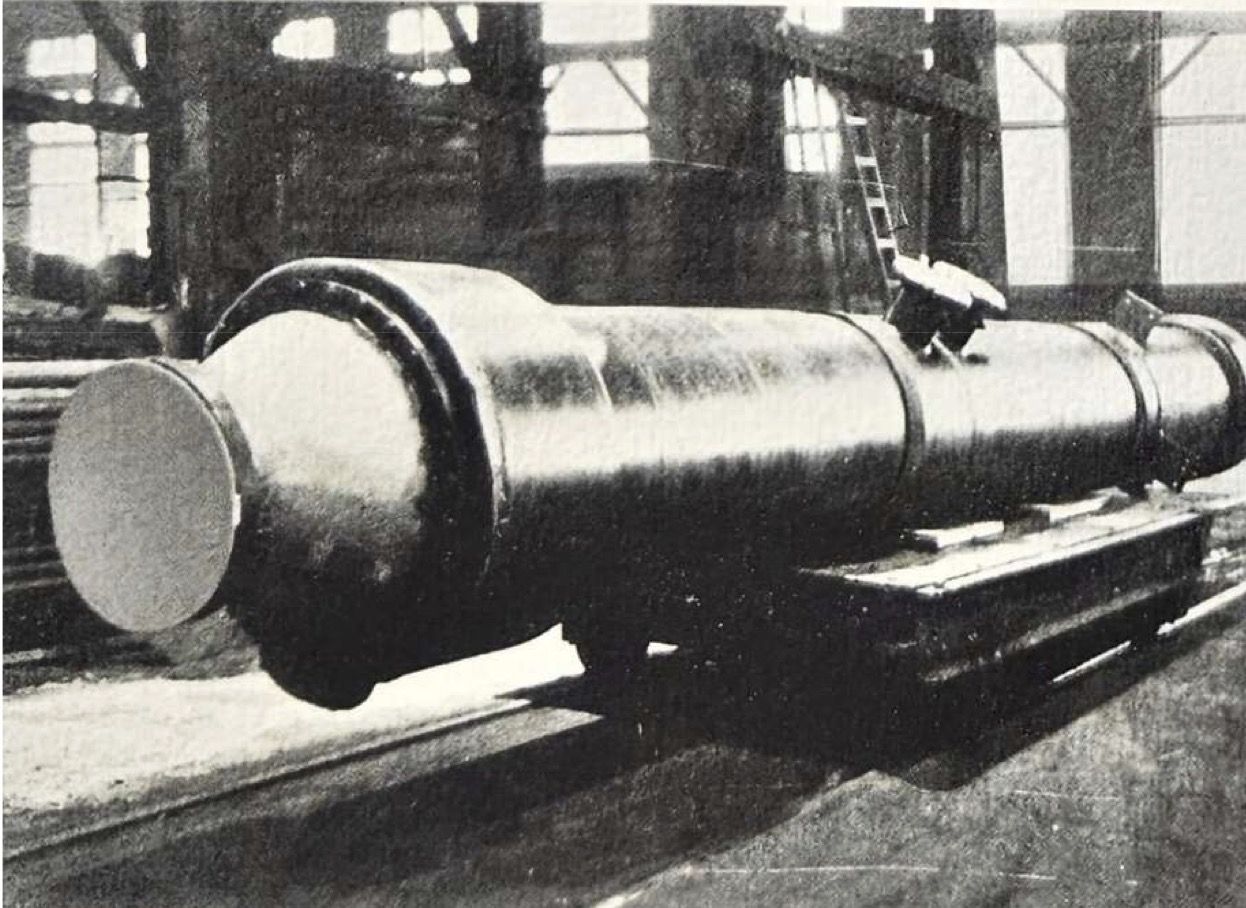
Views of assembling and testing of internal floating head (refinery type) heat exchangers. These vary in size from the smallest to the largest shippable units, in operating pressure ranges from atmospheric to several hundred pounds.
Views of assembling and testing of internal floating head (refinery type) heat exchangers. These vary in size from the smallest to the largest shippable units, in operating pressure ranges from atmospheric to several hundred pounds.
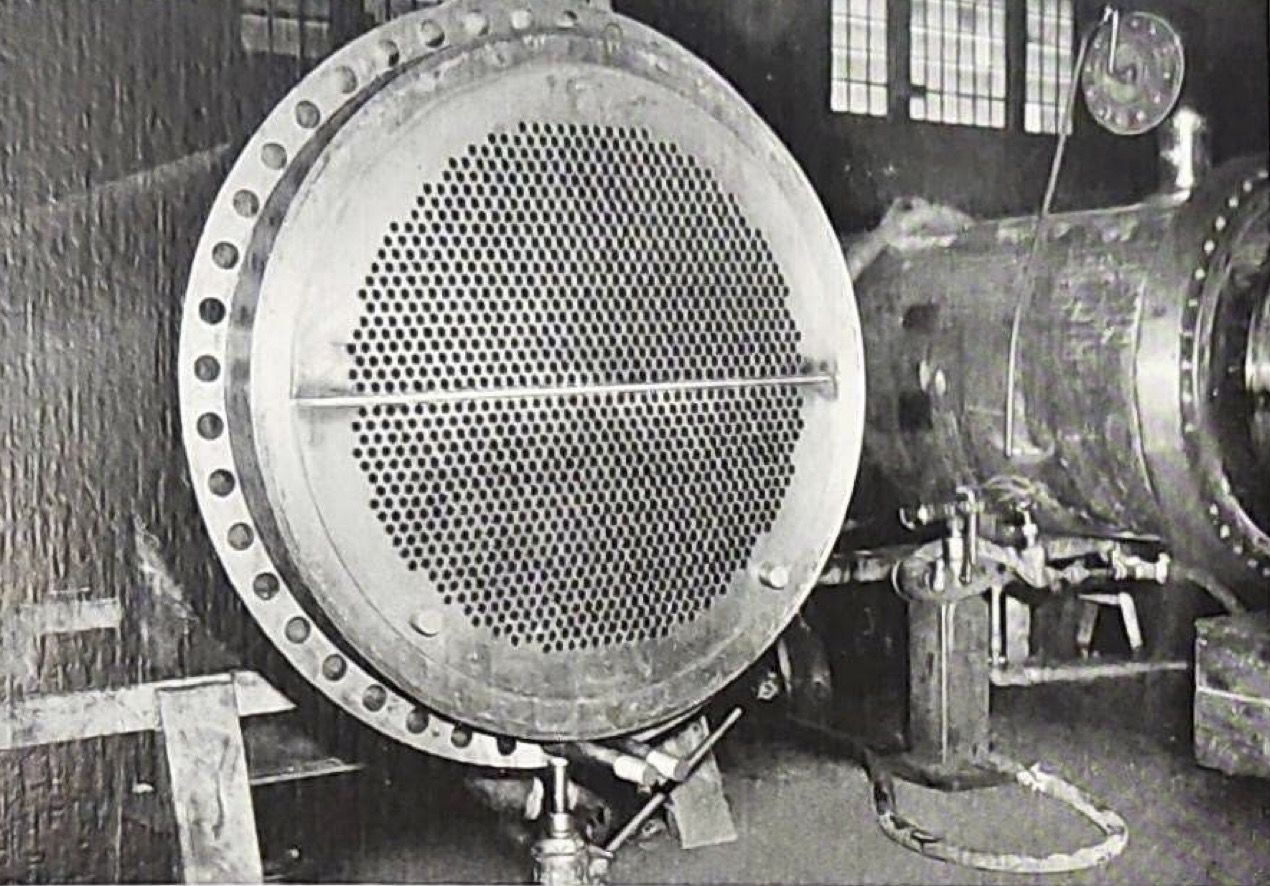
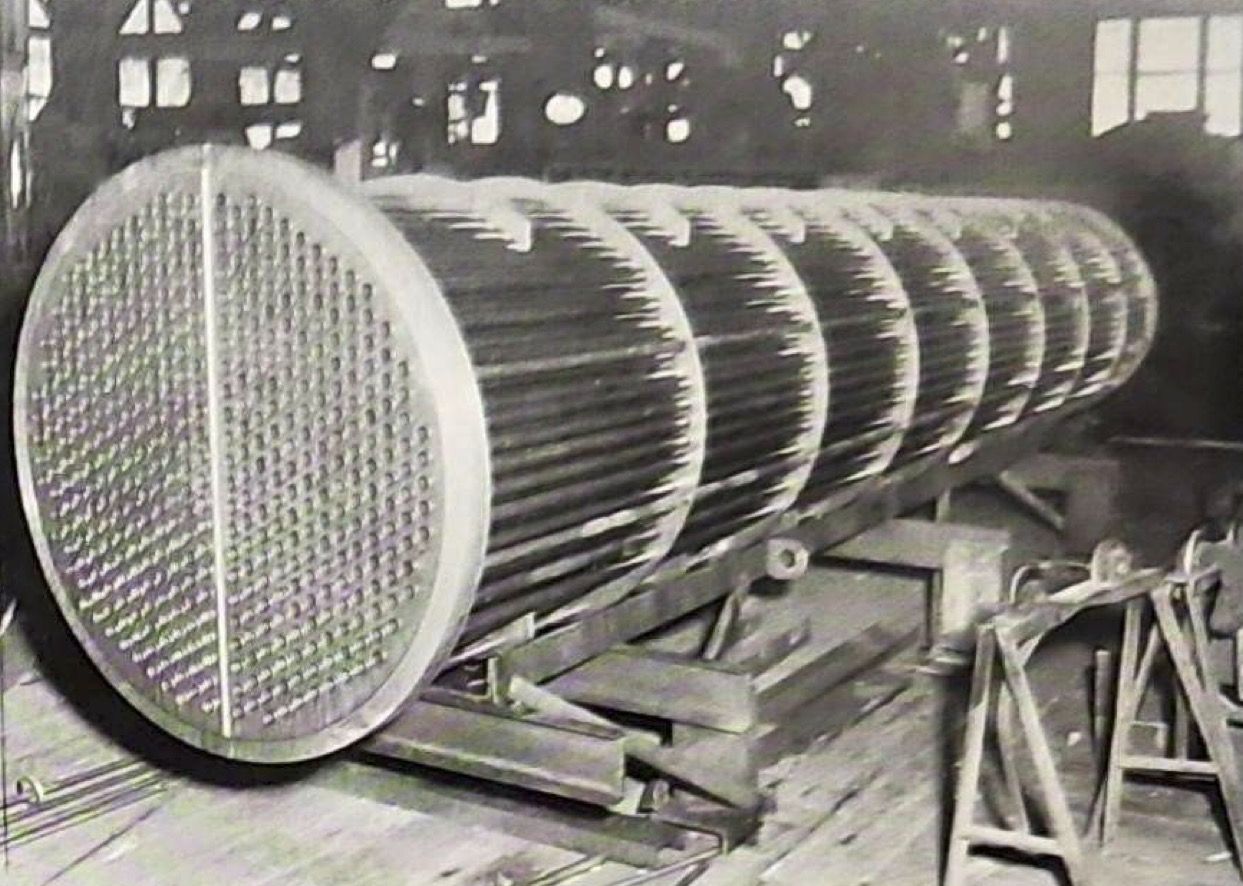
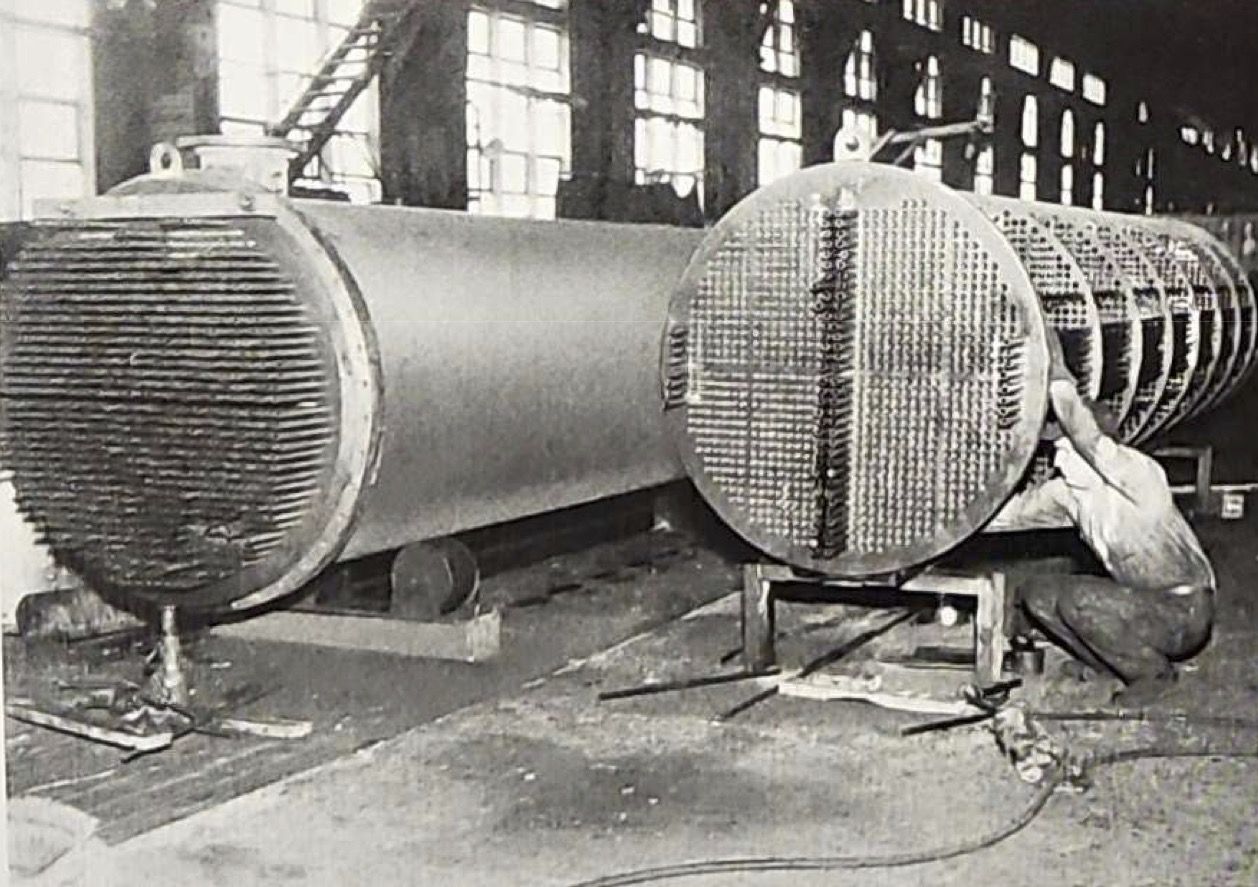
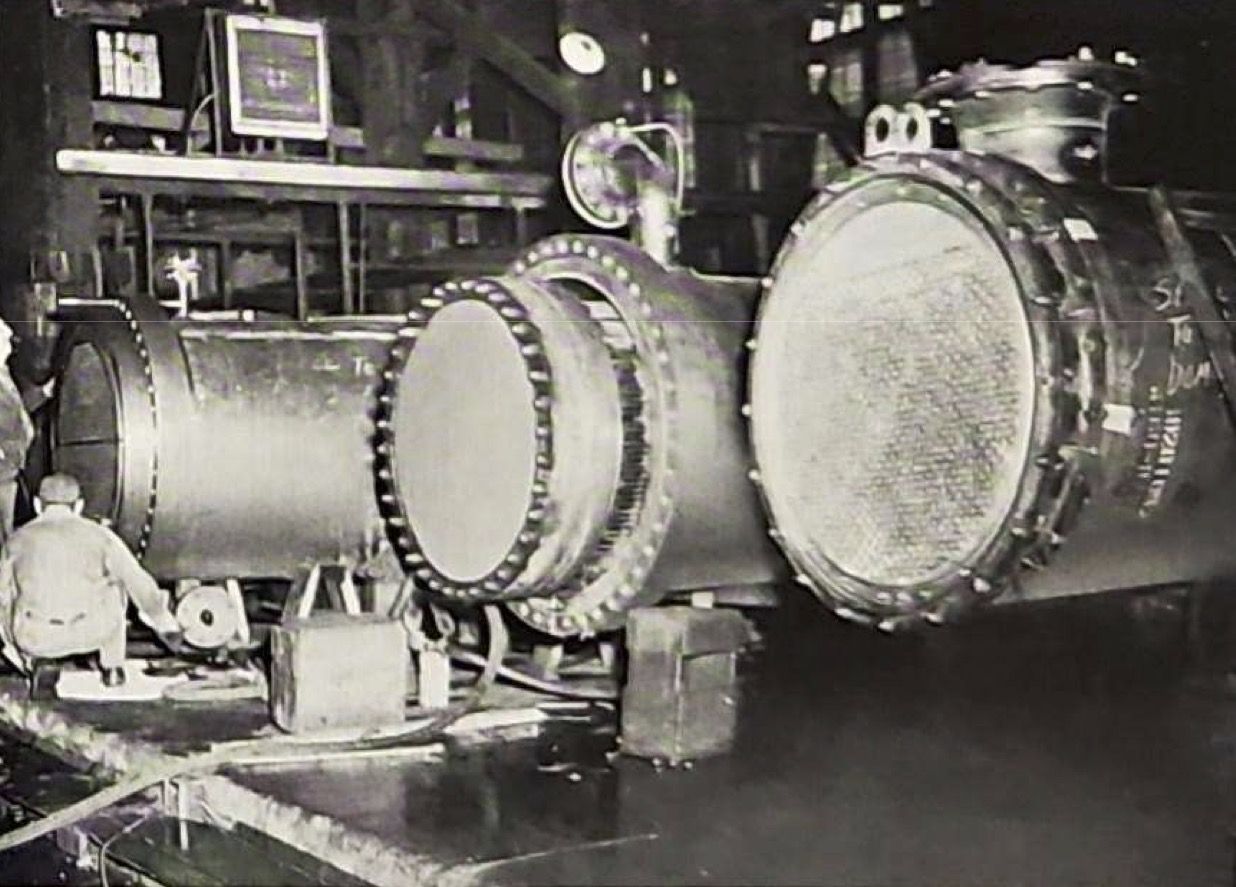
Simplicity of design, rugged construction
Strong Acid Coolers, as shown here, reflect the simplicity of design and ruggedness of construction that Cyclotherm builds into their heat exchangers.
Acid Passes through the tubes by means of simple cone type channel headers for inlet and outlet connections. Heavy wall (14ga) 316L tubes are TIG welded to the tube sheets for strength, positive seal and fair entry. Seal rolling to eliminate backside crevice is performed after welding. Design criteria for acid flow calls for 3 ft/sec. max velocity and 80°C max metal temperature which allows inlet acid temperature of up to 230°F. The shell side containing cooling water, is segmentally baffled and designed to limit water velocity to approximately 4 ft/sec. Cooling water should be cleaned and treated for scale prevention containing minimum chlorides or other halides which are deleterious to stainless steel. Inlets are installed on distribution belts which act as expansion joints and provision is made for cooling the tube sheets at inlet and exit. This cooler design can be utilized either vertically or horizontally.
Cyclotherm has a wealth of experience in the design and fabrication of gas exchangers for acid plants in any required material. The unit pictured below for SO2 exchanger service, is a typical example.
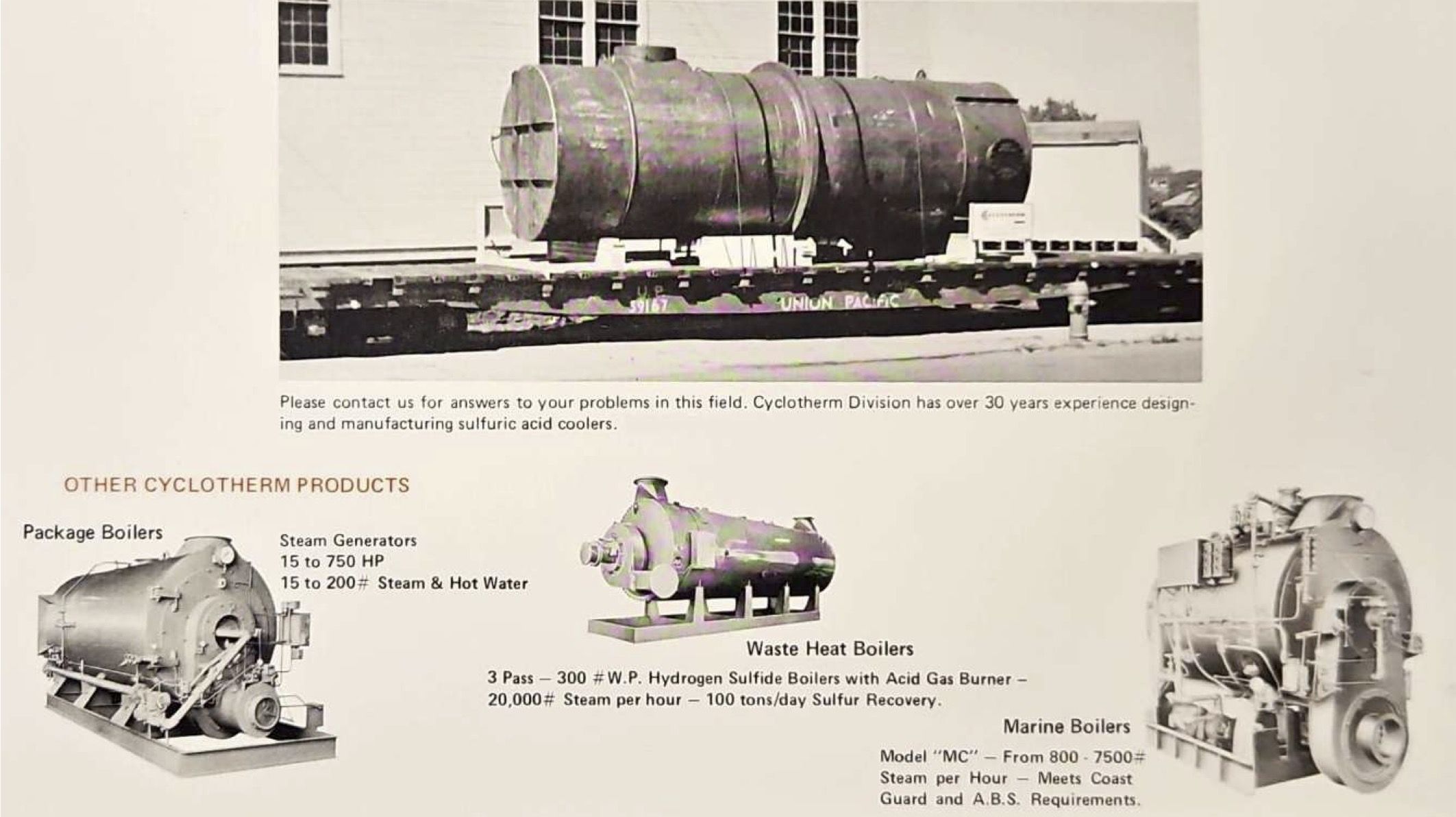
Digester Heater
Cyclotherm has a package unit for sewage sludge heating. The unit is a combination heat exchanger with an integral source of heat together with provisions for utilizing heat from natural gas engines. Complete automatic operation is provided. The Cyclotherm method of combustion is primarily responsible for the high efficiencies realized by this heater. The Cyclotherm burner, an integral part of the unit, provides automatic conversion from sewage gas to an auxiliary fuel. In addition to the high efficiency and flexibility, this unit is characterized by compactness, low cost of maintenance, and ease of control.
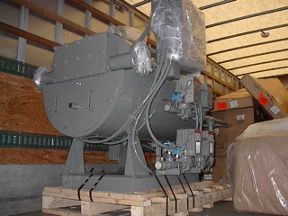
Cyclotherm Digester Heater ready for shipment.
How it works
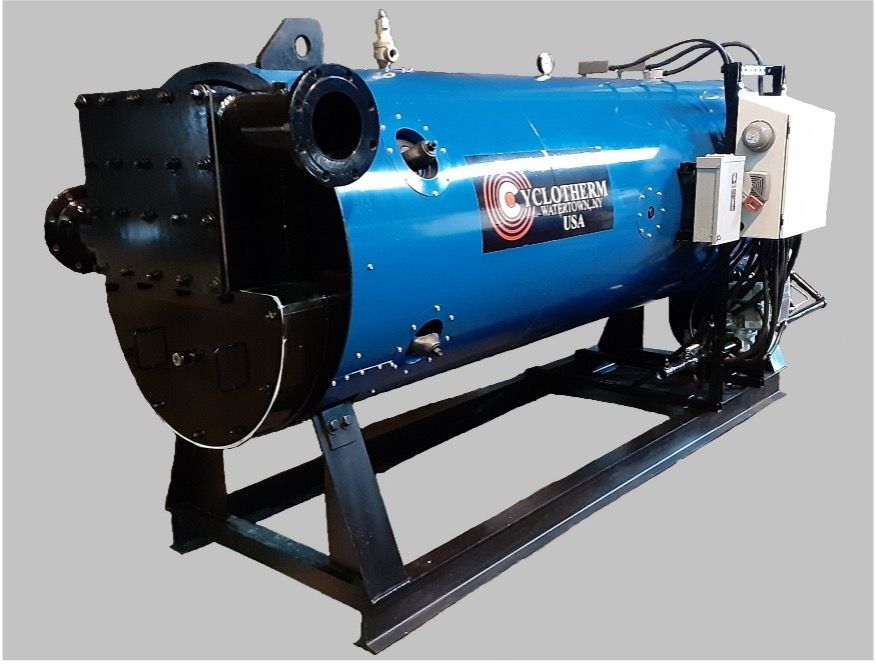
Either front sludge connec1ons or rear sludge connec1ons can be furnished.
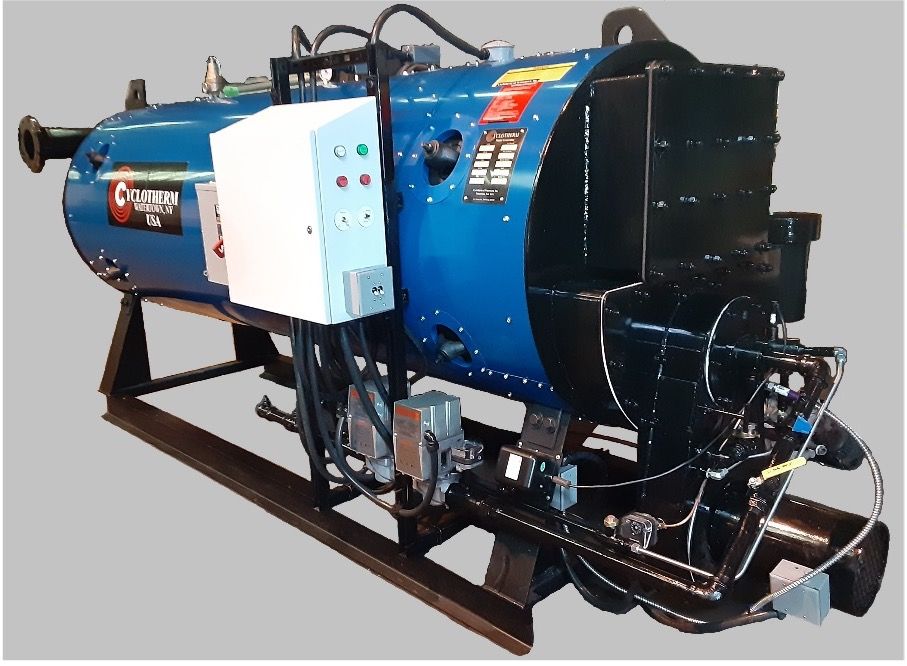
All metal drip-proof control cabinet, factory wired and tested.
Space Requirements
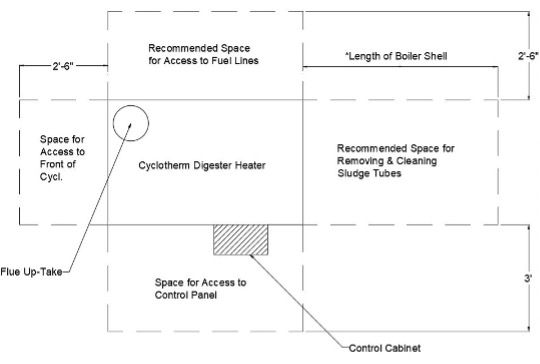
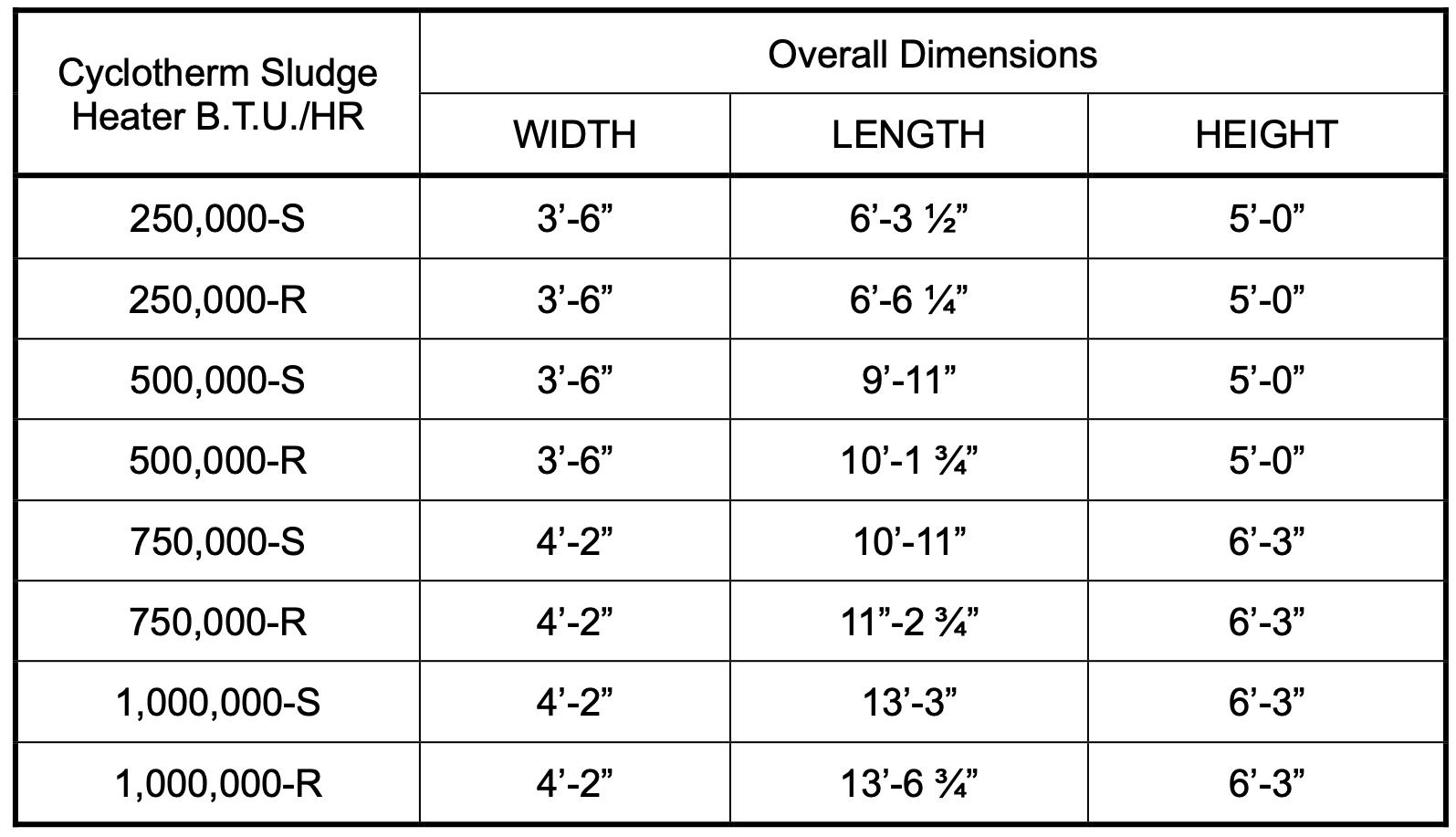
Advantages of the Cyclothem Heat Transfer System
The Cyclotherm unit accomplishes complete combustion of the fuel, resulting in highly efficient transfer from fuel to useful heat.
The unit, being relatively small in overall dimensions, occupies very little space where installed.
A completely assembled, test fired unit is delivered to the customer.
Conveniently located handholes, removable one-piece front and rear covers and a front flue box cleanout and relief door provide for speedy inspection and maintenance of all parts of the unit. Removal of the front and rear covers allows access to all sludge tubes.
Complete combustion of the fuel results in the need of only a simple flue vent instead of a stack, exhaust fan and motor.
A high rate of water circulation within the unit, effected by the simple two-pass construction results in a faster rate of heat transfer.
The ends of the steel sludge tubes are welded in place providing a leak-proof joint and meeting the ASME boiler test code.
Each unit requires only one low horsepower motor.
The furnace tube is continuously swept clean by the cyclonic movement of the air.
Refractory lining is not needed in the furnace tube. Only the burner head, rear cover and furnace extension require protection from the flame.
Standard fittings and connection are used through the unit, and all parts in the control panel are of standard design.
Hot water from the unit can be used to heat the control building.
The unit, being completely assembled on a steel base, requires no special excavation of foundation.
The Cyclotherm burner is designed to burn sewage gas, service gas or light oil or independent operation of any combination of two fuels. Automatic conversion from one fuel to another is provided.
In case of any lack of fuel, water or gas, the entire unit is automatically shut down.